Safe Torque Off (STO)
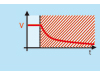 |
- Safe Torque Off (STO) Stop category 0 in accordance with ICE 60204-1: Safe drive torque cut off
|
|
Safe Stop and Safe Drive Interlock (SS1)
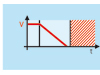 |
- Safe Stop and Safe Drive Interlock (SS1) Safe Stop 1 Stop category 1 in accordance with ICE 60204-1: Safely monitored stop, control or drive controlled with safe drive torque cut off
|
|
Safe Operating Stop (SS2, SOS)
 |
- Stop category 2 in accordance with ICE 60204-1: Safely monitored stop with safely monitored standstill at controlled torque
|
|
Safely Limited Speed (SLS)
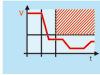 |
- If enable signal is given a safely limited speed is monitored in special operating mode
|
|
Safely Monitored Direction (SDI)
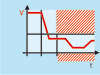 |
- A safe direction (clockwise, counterclockwise) is also monitored in addition to safe motion
|
|
Safely Monitored Position (SMP)
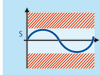 |
- A safely limited position range is also monitored in addition to safe motion
|
|
Safe Inputs/Outputs (SIO)
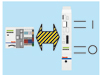 |
- Dual-channel safety peripherals can be connected to the drive and made available to the controller via the safety bus
|
|
Safe Maximum Speed (SMS)
 |
- The maximum speed is safely monitored irrespectice of the mode of operation
|
|
Safe Braking and Holding System (SBS)
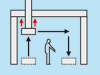 |
- The safe braking and holding system controls and monitors two independent brakes
|
|
Safe Door Locking (SDL)
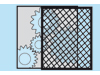 |
- When all the drives in one protection zone are in safe status, the safety door lock is released
|
|
Safely Limited Increment (SLI)
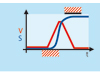 |
- If enable signal is given a safely limited increment is monitored in special operating mode
|
|
Safely Monitored Deceleration (SMD)
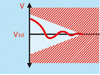 |
- Safely monitored deceleration ramp when stopping with predeternining characteristics
|
|
Safely Limited Position (SLP)
 |
- Monitoring of safe software limit switches
|
|
Safe Communication (SCO)
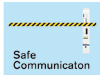 |
- Selection/deselection of safety functions and transfer of process data (e.g. actual position values) via sfety bus
|
|